Drive Train
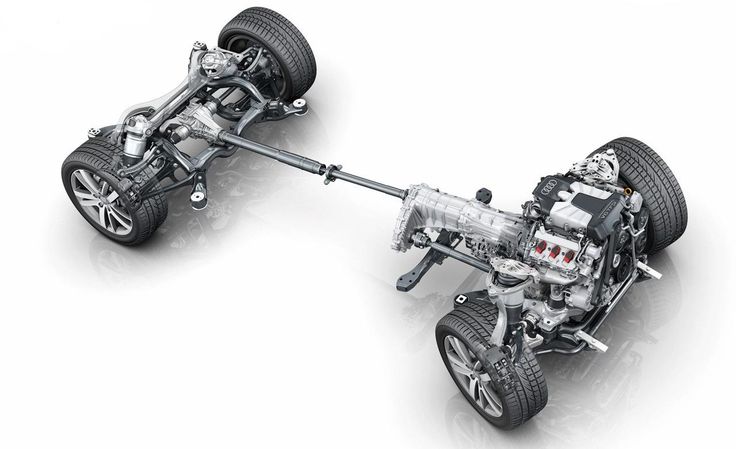
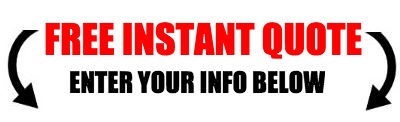
Regardless of whether you drive a 500-hp sports vehicle or a 96-hp economy hatchback, all that strength under your vehicle's or truck's hood is futile if the motor's torque doesn't get to the drivewheels through a perplexing labyrinth of riggings.
Actually, the drivetrain might be the least seen piece of a vehicle. New advancements in four-haggle wheel drive have just exacerbated that disarray for some drivers. Here's a preliminary to help clarify that puzzle under the wood planks: what truly happens when you push down on the quickening agent.
Despite the fact that front drive can be found in such works of art as the 1929 Cord, the overwhelmingly famous present day design depends on the 1959 Mini. Its maker, Sir Alec Issigonis, put the little motor transversely- - sideways- - in the engine, mounted the transmission and differential in one unit called a transaxle, and introduced that underneath and to the back of the motor. While some front-drivers have a longitudinally- - front-to-raise - mounted drivetrain, every one of the segments are still forthcoming. Since the front wheels must direct just as impel, they are associated with the pivot halfshafts by means of complex general joints, called steady speed joints, which can transmit control easily while seriously explained.
The activity of any transaxle is actually equivalent to that of any transmission. The thing that matters is this: Instead of being associated by means of a long driveshaft to the back hub, the transmission's yield shaft drives a huge apparatus that cross sections straightforwardly with the differential's ring gear. What's more, the differential itself (which would be mounted on the back pivot in a rwd vehicle) is situated in the transaxle lodging, mounted parallel to the transmission. As power is applied, the differential circulates it to the two front wheels by means of halfshafts.
CVTs are picking up fame and are utilized in a few new Fords, Saturns and Audis. Rather than gears, the CVT utilizes a belt between two pulleys. One is driven by a pole from the motor, different drives a pole to the differential unit and drive axles. The two pulleys are part with the goal that their parts can slide nearer together and more distant separated. As the belt rides higher and lower in the pulleys, the successful rigging proportions between the driving and driven shafts change.
Still the work of art, back drive was fundamentally the main drivetrain framework for a long time. A longitudinally mounted motor, with the transmission blasted legitimately to it, sends control through a driveshaft to a differential unit at the back hub. The differential turns the power 90° and sends it to the back wheels. (A few sports vehicles, for example, Corvettes, Ferraris and Porsches place a consolidated transmission and differential- - or transaxle- - in the back.)
The driveshaft associates by means of burden type widespread joints and a splined development joint to take into consideration vertical and longitudinal suspension development.
The gearbox is mated to the motor by means of a spring-stacked grip plate looked on the two sides with rubbing material. The grasp must be separated to change gears, and the transmission must be in Neutral, or the grip withdrew, for the vehicle to be halted while the motor is running. The transmission comprises of an information shaft from the motor and a yield shaft to the drivewheels. The information apparatuses can slide to and fro to work with their yield mates. Synchronizer cones between the sliding apparatuses and shaft permit smooth moving. Turn around gear is without anyone else shaft.
An oil-filled torque converter that duplicates motor torque inside the transmission bellhousing permits some slippage so the vehicle can be halted while the motor runs. A grinding grasp incorporated with the focal point of the converter bolts its information and yield shafts to a similar speed for expressway cruising. PC controlled water powered weight chooses which blend of riggings inside a few planetary sets can pivot, changing the proportions between the info and yield shafts.
While cornering, the outside wheels cut a more extensive bend than within. The differential needs to guarantee that the outside and inside wheels are permitted to turn at various velocities—subsequently the name—while as yet providing capacity to the two wheels. The fundamental differential lodging contains a huge ring gear that cross sections with a little pinion gear driven by the driveshaft. The apportion between the ring and pinion gear is known as the last drive proportion or back pivot proportion. The ring gear additionally turns a bearer containing oppositely coinciding arachnid equips that permit the left and right hub shafts to turn autonomously. Drawback: The wheel with the least footing cutoff points control applied to the street.
The idea of furnishing footing to the nonslipping drivewheel with a restricted slip differential goes back in any event to the late 1950s. In spite of the fact that there are presently numerous wrinkles to the old topic, the fundamentals are the equivalent. The creepy crawly equips are precisely connected to share torque paying little respect to conditions. This should be possible basically by including spring-stacked grasp packs that keep the bug gears from turning. Power at that point streams to the two wheels to the furthest reaches of the grasp packs' ability. The creepy crawlies can likewise be pneumatically or electrically bolted together—yet this annihilations the differential capacity.
From a footing perspective, the best of all universes is when both front and back wheels are moving the vehicle. In any case, the front and back axles pivot at various rates with the exception of when driving in a consummately straight line. So the main way both can control the vehicle on dry-street turns is if there's a differential between them. (On elusive surfaces the tire slippage makes up for the wheel-speed contrasts.)
Numerous awd vehicles share a lot of their drivetrain with comparable front-drive models yet include a conservative focus differential, driveshaft and back differential. Four-wheel-drive vehicles use an exchange case set after the transmission that guides capacity to both the front and back axles when required. At the point when connected with, the exchange case drives two separate driveshafts that work singular differentials. No middle differential is utilized on evident 4wd vehicles going rough terrain in 4wd mode.
Two decades from now, you can anticipate that that the power should move your vehicle will be electric. It will probably have a generally little electric engine for each wheel, and the ideas of front-, back and all-wheel drive will get out of date. The gadgets will have the option to guide capacity to any one wheel, to all wheels simultaneously, or to any blend. Either a hydrogen energy unit or an inside burning motor running on hydrogen turning a generator will supply the power. As energy unit improvement costs are as yet stunning, an increasingly monetary option may be to supplant corner stores with hydrogen filling stations.
This is a differential without any riggings. The information shaft from the transaxle (at the front haggles) yield shaft to the back wheels each convey a progression of plates that are then again entwined and firmly divided. every one of the plates swim in an extraordinary liquid that moves control from the contribution to the yield plates when required. In the event that the front-drive wheels start to slip, their pole and plates turn more rapidly than the others. This speed differential inside the lodging agitates and warms the liquid, which thickens it and all the more firmly bonds the substituting plates. Some torque is currently sent to the grippier wheels until turning ones recover footing.
The Torsen goes back to 1983. From that point forward it has been utilized by different carmakers, including Audi and Hummer. The Torsen duplicates what torque is accessible from the hub that is beginning to turn or lose footing, and sends it to the more slow turning pivot with better footing. The riggings permit a torque-inclination proportion of 4:1, which implies they can convey four fold the amount of capacity to the nonslipping pivot than can be bolstered by the slipping hub. One major bit of leeway of Torsen frameworks is that since they are absolutely mechanical, they respond rapidly to slip.
This is a different gearbox mounted behind the transmission. Power goes to the exchange case to be coordinated to the back wheels just or to both front and back. A different driveshaft interfaces the exchange case to a differential in the front pivot. Most move cases likewise offer two gear proportions, for a High and Low range. While numerous vehicles still have a physically drawn in move case, a few currently offer electrically initiated commitment. Call us for problems needing engine repairs or other needed mobile mechanic services.